Imagine an enterprise that runs several geographically dispersed factories. The company has to monitor utilization of hundreds of various machines and seeks ways to optimize the process since traditional report-based methods don’t seem to work well. Despite the thorough observations of process operators, line supervisors, shop managers and factory managers, the data gathered with traditional methods is not always reliable.
Luckily for the enterprise, we are ready to present a solution that addresses this challenge and share our IoT development experience. But first, let’s see what is actually wrong with the report-based way of monitoring machine utilization.
Report-based machine utilization monitoring and its drawbacks
Monitoring equipment utilization with traditional report-based methods, process operators track machines’ uptime, as well as planned and unplanned downtime. They fill in the reports and pass them over to a superior who aggregates the utilization metrics from the stations and calculates key performance indicators, like OEE and TEEP.
With report-based methods, however, enterprises face the following issues:
- The process is manual and time-consuming.
- The collected data is apt to human errors, therefore, inaccurate.
- It is impossible to react to the issues in real time due to the lack of real-time machine data.
For enterprise managers, the process seems even more overwhelming, considering the need to deal with the data from several geographically dispersed factories.
To address the challenges bound to monitoring machine utilization, manufacturers turn to Industrial IoT. Let’s see why IoT-based approach is a game changer for the enterprises practicing distributed manufacturing.
IoT-based equipment utilization monitoring and its benefits
Industrial IoT solutions enable manufacturers to view utilization measurements in real time without physical access to machines. Monitoring machine utilization starts with collecting the required data with the help of sensors. Sensors measure various machine operating parameters (e.g., run time, actual operating speed, product output, etc.) and transmit the data to the cloud for processing. The cloud aggregates the data and develops it into valuable insights by applying analytics tools. After the data is analyzed, the results are visualized and displayed to the enterprise managers. Now they can view the machine utilization metrics on a single dashboard. To get a deeper understanding, check out how utilization monitoring works in a sample smart factory application.
And it’s not the only benefit. With the IoT-based approach, enterprises running distributed connected factories also get:
Instant access to information
With connected sensor-equipped machines, manufacturers get instant visibility into machines’ performance. It enables them to monitor key utilization indicators in real time and react to failures and outages instantly. Whenever a problem arises on the line, an IIoT solution provides a detailed insight into the problem and helps to identify its root cause, so manufacturers can put the machine back on track more easily and quickly.
Precise visibility
An Industrial IoT solution provides details on how the machines are operating across the enterprise. It displays instant updates about KPIs, including OEE and TEEP. At the enterprise level, it gives managers real-rime visibility into how each factory is performing. At the factory level, shop managers get real-time detailed data from the equipment, so they can better understand how efficiently the equipment is functioning and take better decisions to drive throughput and increase productivity.
IIoT provides factory-wide visibility into equipment performance and notifies users about performance reduction
Detailed analytics
With IIoT, the data about what happens on the factory floor is stored, analyzed and developed into informative insights. Data analytics tools are applied to analyze real-time machine activity data – what machines do, when they idle, when they fail to produce. Additionally, data analytics tools fetch historical data about equipment’s performance from a maintenance database. After the data is analyzed, the results are visualized and displayed to the enterprise COOs. Now they can leverage the detailed metrics to optimize manufacturing process, forecast demand, increase product quality and prevent equipment failures.
IIoT provides near real-time visibility into an asset's OEE and displays the effectiveness dynamics
OEE calculation
An Industrial IoT solution transforms streams of sensor data into comprehensive insights about the equipment efficiency by calculating OEE and identifying a particular loss behind the reduction in the effectiveness. In the table, we present which losses for what equipment types can be measured by an IIoT solution.
It’s important to highlight that although an IIoT solution calculates the top KPIs quite precisely, even better results are achieved when IoT-based and report-based methods are applied simultaneously. Reports can be used to explain specific cases and provide a clearer picture of how well the equipment is functioning by comparing the measurements fetched by an IIoT solution and those acquired by a human.
Connecting different types of machines
No massive change comes without a massive challenge. Implementing an IoT solution, manufacturers have to consider the diversity of the equipment at the geographically dispersed factories and find ways to efficiently connect non-computerized machines, machines with computer numerical control (CNCs), machining centers, and robots to a single IoT solution. Let’s dwell on each type in more detail.
Robots
Among other types of equipment, industrial robots are integrated with an IoT solution with relative ease, since they have embedded sensors and built-in Ethernet port. The machine-to-cloud connection in such case is carried out through an Ethernet port via an IoT gateway.
CNCs and machining centers
The following ways are used to connect CNCs and machining centers to the cloud:
- Via an Ethernet port
- Via a serial-to-Ethernet converter
- Via a machine’s PLC
The choice of the relevant method depends on the features of a machine.
The first method is applied to newer machines, embedded with an Ethernet port. In such case the data is transmitted to the cloud through an Ethernet port via an IoT gateway. This way, whenever a machine’s cycle starts/ends, the spindle turns on/off, etc., the corresponding data record is sent through an Ethernet port to a PC and then to the cloud.
Second, if a machine lacks Ethernet connectivity and uses a serial protocol, say, RS-232/422/485, these protocols need to be converted to Ethernet protocols to ensure free data transmission across TCP/IP networks. The data record in such case is passed through a serial-to-Ethernet converter to the cloud.
The third method implies tracking digital signals from a machine’s PLC. In such case an IoT gateway is used as an interim component to track signals from the PLC, convert the protocols and transmit the data to the cloud.
Non-computerized machines
Non-computerized machines often hinder the adoption of IIoT technologies. Unlike modern industrial equipment, they do not have built-in communication and processing units, therefore, can’t ensure machine-to-cloud communication.
Since it is not possible to upgrade such machines to the level when they can communicate with the cloud, the alternative is to attach sensors directly to machines and use IoT gateways. IoT gateways act as go-between for sensors and the cloud, accepting various industrial input signals (TC, RTD, mA, mV, frequency, etc.) and supporting a wide range of communication protocols, say, MQTT, allowing to aggregate, filter and transmit sensor data to the cloud.
What if there’s a control system?
Industrial equipment can be managed by a SCADA. In such case the possibility of integration through SCADA depends on whether SCADA is capable of transmitting the needed data to the cloud or not. If so, the integration with the cloud can be performed via SCADA. Otherwise, when SCADA’s purpose is, say, checking equipment’s health, and it can’t provide the cloud with enough data, manufacturers have to think about the ways to ensure parallel connection of the machine both with SCADA and with the cloud.
Let’s brush it up
Monitoring machine utilization across geographically dispersed factories with IoT-based solutions has substantial benefits. At the same time, as our IoT development experience proves, enterprises practicing distributed manufacturing have to think about the ways to integrate different types of equipment with an IIoT solution. The integration is not trivial and requires a careful study of the legacy equipment.
Before implementing an IIoT solution, take the time to properly assess legacy infrastructure and evaluate how old the equipment is, what steps should be taken to upgrade it and how much time and money the upgrade will take. This is a crucial point that will help you to find a cost-effective IIoT solution.
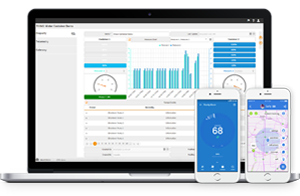
From roadmapping to evolution – we’ll guide you through every stage of IoT initiative!