Geodis supply chain survey (2017) revealed that improving end-to-end supply chain visibility is one of top three goals for supply chain managers. The same research states, however, that only 6% of businesses have gained complete visibility into their supply chains, 77% of the respondents claiming to have no or restricted visibility and 17% having visibility into one or two supply chain segments.
To address supply chain visibility issues, improve product availability, stay connected with the partner networks, and uncover new ways of enhancing supply chain operations, manufacturing enterprises resort to technological innovations.
Considering the fact that by 2020, one-third of manufacturing supply chains will become technology-driven, we are here to answer common questions supply chain managers may be concerned about as they shift to smarter supply chain management.
First off: what is the reason behind introducing technologies into the manufacturing supply chain?
The primary reason behind introducing technological innovations into the supply chain management is mitigating uncertainty. Similar to landing a plane relying on the reports about past landings rather than accurate, real-time data from the radars, enterprises use a mix of after-the-fact spreadsheets and ERP findings as the basis for supply chain decision making.
The key factor that makes these methods unsuitable for large-scale supply chain management is relying on manual data input, which often results in:
- High probability of error: Coopers and Lybrand estimated that roughly 90% of spreadsheets comprised of more than 150 rows contain errors.
- Possible delays: manually extracting data from different departments, consolidating and integrating it is time-consuming. Hence, decisions are often made based on outdated information.
- Absence of data: with manual methods, it is rarely feasible to track every movement of every item across multiple shops and warehouses. One can never be sure if the availability of an SKU has changed between the moment it was tracked and the moment an employee checks a spreadsheet.
- Lack of individual items’ identification: with manual methods, it is impossible to track the detailed information about individual items within a particular SKU. For instance, a warehouse worker knows they have 978 packs of a perishable product at a warehouse. However, the production date for each pack is unknown, hence it’s impossible to identify, which of them should be sold first.
What are the technologies that enable smart supply chain management?
The main technological enablers that drive productivity and increase visibility along the manufacturing supply chain are RFID and IIoT.
RFID
RFID systems consist of three components: RFID tags, RFID antennas and RFID readers.
RFID tags are microchips carrying encoded digital data about the objects they are attached to (e.g. type, description, manufacturer, etc.). RFID tags – be they passive or active - can be attached to any physical surface, from raw materials to packages and crates.
RFID antennas catch radio waves from the readers to supply energy for the tags and enable them to transmit the identification data they contain to the readers.
RFID readers are used to read the data from the tags. They can scan the number of tags over distance. Scanned by an RFID reader, a tag emits a radio signal carrying its ID. The reader converts radio waves emitted by RFID tags into digital information and relays it to the cloud for storing, processing and analysis.
Industrial IoT
By analyzing the data fetched from sensors and/or RFID tags, the Industrial IoT helps to gain higher visibility into the supply chain processes. For instance, analyzing the data from RFID tags attached to the inventory items and sensors installed at a smart warehouse, a supply chain management system can provide warehouse workers with real-time data about the location, the status and the condition of each inventory item, notify workers of inbound deliveries, provide insights into the use of the warehouse equipment, etc.
At the same time, with advanced data science techniques, the Industrial IoT lays a solid foundation for the automation of supply chain processes. For instance, an IIoT-based supply chain management system can forecast the amount of the inventory needed for the upcoming production cycle, recommend the optimal replenishment date and even automatically send a replenishment order to a supplier.
To enable mutual data sharing, IIoT solutions are integrated with other enterprise systems (MES, ERP, WMS, PIMS, DCS, etc.). For instance, an IIoT solution can access maintenance department’s data in order to ensure the state of shipping vehicles is appropriate or provide an accounting department with real-time data about assets required for the enterprise’s annual reports.
What segments of the connected supply chain can be monitored?
With RFID and IoT, every segment of the supply chain becomes a data point, providing supply chain players with real-time insights into the statuses, locations and conditions of parts and materials, work in progress and finished goods, pieces of equipment and vehicles. IoT-driven supply chain management solutions provide the data about:
- Materials and components on the supplier side
An enterprise and its suppliers should agree upon rolling out an RFID system at the supplier’s site or getting access to the data from the supplier’s IoT system to get real-time information about the supplier’s inventory levels, delivery statuses, schedules and routes. This way, manufacturers can timely react to the changes in suppliers’ manufacturing operations, hence, reduce risks of delayed and unfulfilled orders.
- The condition of goods in transit
Before IoT came into play, the condition of the transported goods could only be checked once they arrived at the delivery point. Now vehicles can be equipped with temperature, humidity, vibration and shock pulse sensors to allow manufacturers view information about the condition of the goods en route.
- Inventory at a manufacturing facility and a smart warehouse
With inventory items labeled with RFID tags, inventory specialists and warehouse workers get real-time insights into the locations, statuses and flows of raw materials, and finished goods as they move within and between facilities.
- Delivery to customers
Leveraging the data fetched from RFID systems and sensors installed in the vehicles for monitoring the delivery conditions, manufacturers ensure on-time shipments and proper quality of the transported goods.
What parameters can be monitored?
At each segment of the supply chain, IIoT and RFID are applied for monitoring the following parameters:
- Location
RFID readers fetch the IDs of the tags attached to the objects and relay them to the cloud together with the readers’ IDs and the time of the reading. Knowing the location of the readers, inventory specialists learn the locations of tags. By tracking the tag data by time, workers monitor the movements of each object.
- Condition
IoT helps enterprises to monitor the condition of the goods in transit and at a warehouse to ensure that no goods are damaged. For instance, if a vibration sensor installed in a truck detects that the vibration frequency exceeds the norm, employees get notified of a potential damage. Analyzing historical sensor data, it is possible to conduct a root-cause analysis of the past damages and take measures to avoid them.
- Lifetime
Some industries, e.g. food production, pharmaceutics, electronics, etc., have to deal with sensitive products that require specific conditions to preserve their quality. Once overlooked, they affect the lifetime of the products. With IoT, manufacturers can monitor the conditions influencing lifetime of the perishables by gathering the data from temperature and humidity sensors attached to the inner side of the packages. The IIoT solution analyzes sensor readings, detects if the temperature or humidity level inside the crate deviates from the norm and automatically notifies warehouse workers, truck drivers, or other players involved.
What are the benefits of IoT-driven supply chain management solutions?
IoT-driven supply chain management solutions allow manufacturers to gain:
- End-to-end visibility into the supply chain
Smart supply chain management solutions provide manufacturers with real-time data about the statuses, locations and flows of products at all supply chain segments - starting from monitoring materials and components on the supplier side up until the moment when a final product gets to customers.
- Higher levels of operational efficiency
Real-time visibility allows enterprises to enter a new level of operational efficiency. With the data about the amount of materials on hand, the location of work in progress and the status of the goods in transit, enterprises reduce material search time and costs, as well as achieve higher speed of operations.
- Better customer service
With IoT, enterprises can reduce the time it takes to fulfill customers’ orders and provide them with the data on where their items are and when exactly they will be delivered.
- Optimized inventory management
With real-time data about the quantity, location and movement of inventory items, manufacturers know when they need to restock. It eliminates the need to keep several weeks of inventory on hand, still allowing to maintain high level of customer service.
- More efficient waste management
IoT helps to identify and, hence, mitigate at least five of the seven mudas (wastes, operational activities that add no value) including transportation, inventory, waiting, overproduction and over-processing wastes.
What industries can benefit from applying connected supply chain management solutions?
IoT-enabled solutions bring significant improvements in productivity, operational efficiency and visibility regardless of the industry. Here are just a few examples of the industries already reaping the benefits of IoT-enabled SCM solutions:
Electronics
Supply chains in the electronics industry form some of the most complex systems. They start from mining raw materials, all the way through the production of components and assembling of the final units to transporting them to wholesalers and retailers, until they finally get to end customers. RFID and IIoT can be applied to track the status and the condition of goods throughout these segments.
Hewlett Packard Enterprise EMEA, for instance, has been using Industrial IoT for some years already. The implementation of the IoT-driven supply chain management solutions enabled them to reduce cycle times by 50% over the last two years, as well as increase employees’ engagement and productivity.
Food
Foodstuffs and agricultural products are especially sensitive to temperature changes and other environmental factors as they travel from farmers and cultivators through manufacturing and distribution sites to supermarkets, restaurants and other points.
Deschutes Brewery, for instance, is using an IoT-driven solution to control a product cooling process and eliminate the need for manual temperature readings.
Oil & gas
Once oil and gas are extracted from remote drilling installations, they travel by pipeline, ship, train or truck to oil refineries, gas stations and other destinations. Connected supply chain solutions allow to access tank, pipeline, and equipment data at up-, mid- and downstream stages, thus allowing oil and gas companies to avoid shortages, prevent accidents, and effectively respond in crises.
When to start, where to go?
At the moment there is no out-of-the-box SCM solution that offers plug-and-play configuration. To establish effective supply chain management, manufacturers have to implement custom solutions. Given the complexity of the global supply chain, it makes sense to improve the supply chain management segment by segment – based on the current needs.
For instance, for the manufacturers dealing with sensitive materials, say, nano carbons, it is important to monitor the condition of materials during inbound deliveries. The sensible step would be to start with a solution for inbound deliveries management and use the established infrastructure to expand the solution later, say, for managing outbound deliveries and in-house inventory.
Considering the ever growing complexity of the manufacturing supply chain (70% of manufacturers say their supply chains are very or extremely complex), it proves efficient to turn to an experienced IoT consultant – they will help to choose an optimal IoT vendor and a best-fit solution, as well as properly integrate it with internal corporate systems.
So, what’s in the end?
IIoT-driven supply chain management solutions allow to mitigate inaccuracy and labor-intensiveness of manual methods of supply chain management and planning. Driven by RFID and IIoT, connected supply chain solutions will allow to monitor the delivery of materials and components from suppliers, the condition of goods in transit, the location and movement of goods at a manufacturing facility and a smart warehouse, and the delivery of finished goods to end customers.
See what we offer
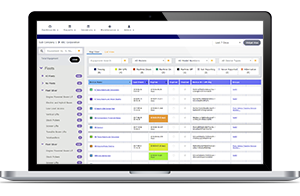
Industrial IoT (IIoT) solutions by ScienceSoft
Are you starting an industrial digital transformation and looking for a reliable and cost-effective IIoT solution? Check out our offer!
See what we offer