Editor’s note: Computer vision offers truly impressive advances for the food and beverage industry. Read on to learn details about its current applications in food sorting, safety control, and standardization. And reach out to ScienceSoft, a custom software development company, for getting accurate custom software solutions to your business needs.
The food industry is in the top ten industries using computer vision for quality control.[1] With automated visual inspection systems becoming increasingly adopted commercially[2], we can watch how image analysis technologies are changing the food production process here and now.
How computer vision is applied in the food industry
Computer vision systems inspect food quickly, objectively, reliably and non-destructively, and they have a potential to take on many monotonous tasks traditionally performed by human inspectors. Apart from quality control, they show great results in product grading and counting.
1. Quality check
Today, it is possible to inspect the quality of a wide range of food products with a computer vision system. Both software and hardware parts of the system should be customized to the specific needs of a food company, including inspection goals and the type of product to analyze.
For example, feature extraction and segmentation algorithms will vary significantly depending on the shape, color and texture of an analyzed object, as well as the surrounding scene (the conveyor belt, a crate) and illumination conditions.
Inspection goal | Products | Objects and features | Technologies |
To detect food contamination |
|
|
Imaging methods:
Image analysis steps:
|
To estimate freshness | Any packed product | The color of a time-temperature indicator (“freshness watchdog”) | |
To check uniformity and grade by quality |
|
|
2. Measuring, counting and sorting
Market analysis shows that all other things being equal, customers prefer apples with a maximum diameter between 75 and 80 mm.[1] However, people would have a hard time trying to accurately evaluate a fruit’s size with the naked eye, while a computer vision system can measure a precise diameter of an apple in a blink of an eye, literally.
Automated counting and sorting system based on image analysis can grade fruits, vegetables, nuts, oysters, etc. according to their shape, size and maturity (for fruits and vegetables), increasing the sorting speed by 10 times compared to humans.[2]
3. Packaging
Automated visual check of a filling level and package labeling is another important application of computer vision in the food industry. Besides that, a visual system can check the freshness of a packed product with the aid of a special ink changing its color with time and at a different speed depending on the temperature.
Benefits of the automated visual inspection
1.Better quality
A study conducted by the Food Marketing Institute and Grocery Manufacturers Association has shown that the average cost of a recall for food companies is about $10 million in direct costs, not to mention brand damage and lost sales.
Microbiological contamination is reported to be the main reason for recall (47%) in 2016 in the U.S., the second being labeling issues (26%). Processing defects and physical contamination are responsible for 13% and 7% of recall cases correspondingly.
Source: http://fortune.com/food-contamination/
We can see that in most cases the reason for recall could be neutralized in the production line with the aid of automated visual inspection.[1]
By timely managing quality issues, food companies reduce consumer complaints, improve brand perception and prevent potential legal problems.
2.Higher productivity
Automated sorting, counting and packaging make the production more efficient. Acting at the speed unattainable by humans, machines also perform these operations with a consistent accuracy.
Food production companies that have already embedded computer vision solutions into the production line confirm this efficiency. For example, Ray Keller, General Manager at Apple King LLC, says that automated visual inspection provides “great grading results and 30% increase in [apple] production”.
3.Lower scrap and give-away rates
If defective products are detected early in the production, they can be rejected before any value is added. For example, it would be better to find a rotten apple before it was packed together with other apples.
Besides that, an automated visual inspection system can precisely count and measure the ingredients to prevent their excessive use. For example, it can control the amount of chocolate topping on a cookie, minimizing the give-away rate.
4.Less labor intensity
Performing simple monotonous tasks at the lightning speed, computer vision systems spare time and labor of human workers who can concentrate on some more sophisticated tasks instead.
Challenges to overcome
Computer vision deals with simple identification, measuring and counting better than human vision. However, to achieve this high level of performance, the inspection conditions should be strictly standardized.
For example, object identification becomes much more difficult in a complex scene. Efficient edge detection and segmentation require a homogenous background.
The same applies to light conditions: insufficient and non-uniform illumination obscures shapes of inspected objects and causes false edge detection.
Trends and expectations
Computer vision is evolving rapidly, offering more accurate and reliable techniques for image enhancement, edge detection and segmentation. Advances in machine learning (convolutional neural networks, support vector machines etc.) allow creating the software able to perform classification of features and objects detected in an image more intelligently. With further refinement of image analysis techniques, the food industry can expect that even more visual inspection tasks will be automated in the future.
References
1. X. Zou, J. Zhao. Nondestructive measurement in food and agro-products. January 2015.DOI: 10.1007/978-94-017-9676-7.
2. D.W. Sun, editor. Computer vision technology in the food and beverage industries. Cambridge: Woodhead Publishing; 2012.
[1] An automated visual inspection system can assess microbial contamination of poultry indirectly by detecting and evaluating its fecal contamination.
Learn more
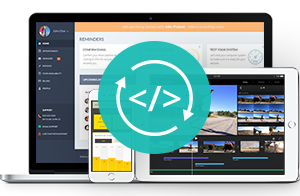
Custom Software Development
Our strong BA team, handpicked developers and proven PM practices get your tasks solved with software that brings maximum benefit and optimal TCO.
Learn more